If You Can’t Measure It, You Can’t Manage It – Peter Drucker
The circular knitting industry struggles with hidden inefficiencies that can significantly impact profitability. Over 100+ installations of Knit-I, we’ve seen firsthand how measuring losses can boost bottom-line profits by 1-2% and increase revenue by 2%—a game changer for manufacturers.
Let’s dive into the three biggest losses in knitting and how tracking them can unlock major savings
LOSS 1: Waste Loss (The Silent Profit Killer)
What is it?
Waste loss is the difference between yarn input and fabric output.
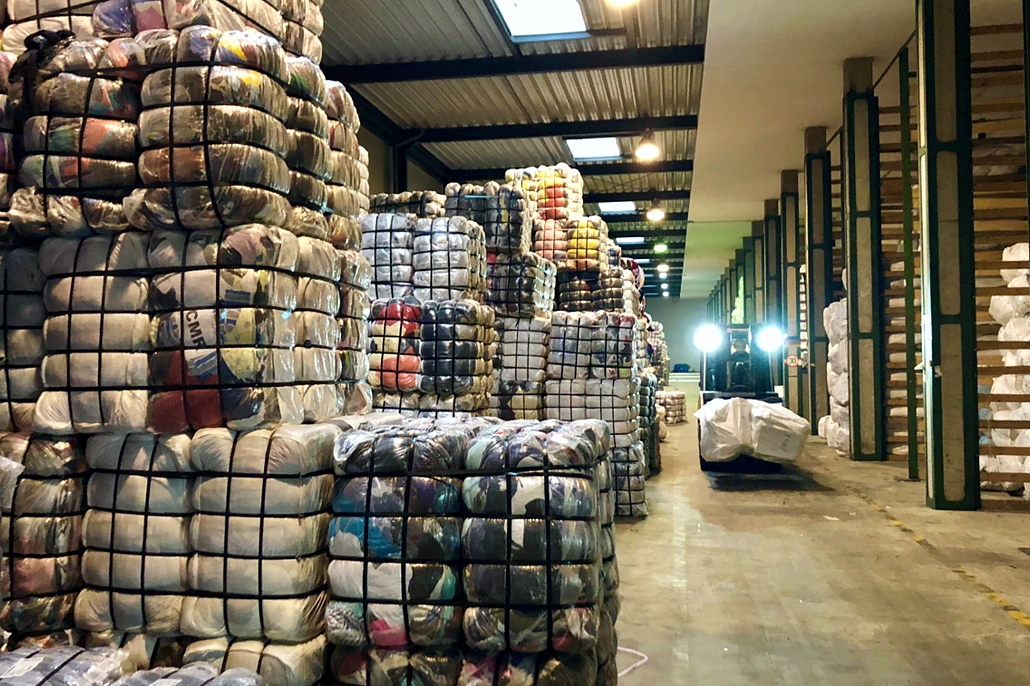
How to Calculate?
Waste Loss = Yarn Used (kg) – (Fabric Sold + Claims)
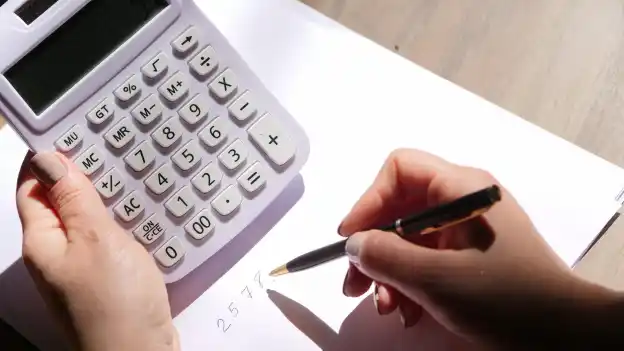
Where Does Waste Go?
🔴 Defective Fabric – Production errors leading to rejected fabric.
🔴 Yarn Wastage – Excess yarn due to poor planning.
🔴 Humidity Loss – Moisture content changes in yarn.
🔴 Fluff & Running Loss – Fiber loss during the process.
🔴 Fabric Setting Time Loss – Time lost adjusting fabric settings.
🔴 Excess Yarn Purchased – Over-ordering leading to dead stock.
🔴 Unsold Fabric – Produced but not sold, tying up cash flow.
Real Example
A factory in Turkey assumed their waste was 3%, but after installing Knit-I, they realized it was actually 7%! Just by optimizing fabric settings and tracking fluff loss, they saved over $100,000 per year!
Pro Tip
Avoid the temptation to add water to increase fabric weight—it’s a short-term trick that damages long-term quality.
LOSS 2: Opportunity Loss (Machines Running Below Potential)
How to Calculate?
📉 Opportunity Loss = Maximum Production – Actual Production
Why Does It Happen?
⚠️ Low RPM Settings – Machines running slower than they should.
⚠️ Frequent Stops – Due to inefficient doffing, yarn setting, and maintenance.
⚠️ Long Service Times – Unoptimized machine servicing.
Real Example
One of our customers had their machines running at 90% of max RPM. By tracking lost time with Knit-I, they identified simple tweaks that boosted efficiency and added $50,000 in profits annually.
Pro Tip
Measuring production in real-time helps reduce opportunity loss by adjusting machine speeds dynamically.
LOSS 3: Premium Quality Loss (Missing Out on Higher Profits)
What is it?
Money lost due to lower-than-ideal fabric quality.
How to Calculate?
Direct Money Quality Loss =
Debit Notes + Lost Premium Price – Market Sale Price

Where It Happens?
⚠️ Lower-Grade Fabrics – Grade B & C fabrics selling at a discount.
⚠️ Debits & Claims – Customer complaints and returns.
⚠️ Inconsistent Quality – Missed opportunities to sell at premium prices
Real Example
A factory in Bangladesh discovered that by adjusting tension settings and humidity control, they reduced Grade B fabric output by 40%—increasing their revenue by 3%.
Pro Tip
Measuring defect rates in real-time helps maintain top quality and maximize revenue.
1. How to Set Up a Waste Measurement System
✅ Record every yarn batch entering the factory.
✅ Track fabric sold from each batch.
2. Calculate Fluff & Running Loss
✅ Weigh yarn before and after knitting.
✅ Measure at least 1000 doffs for accuracy.
3. Minimize Fabric Setting Loss Time
✅ Track loop length, IRO tension, fabric tension.
✅ Continuously optimize machine parameters.
4. Optimize Yarn Purchasing
✅ Use long-term tracking to order the right amount.
5. Measure Defective Fabric Accurately
✅ Log all defects, cut pieces, and Grade B/C output.